Scene Shop Supervisor Levi Galloway, Technical Director D.J. Selmeyer, and Assistant Technical Director Marc White, from the Department of Theatre at Michigan State University, write about the technical seminar they hosted Oct. 12 for Theatre students. The seminar took place on the set of “Clue” at the Pasant Theatre in the Wharton Center for the Performing Arts.
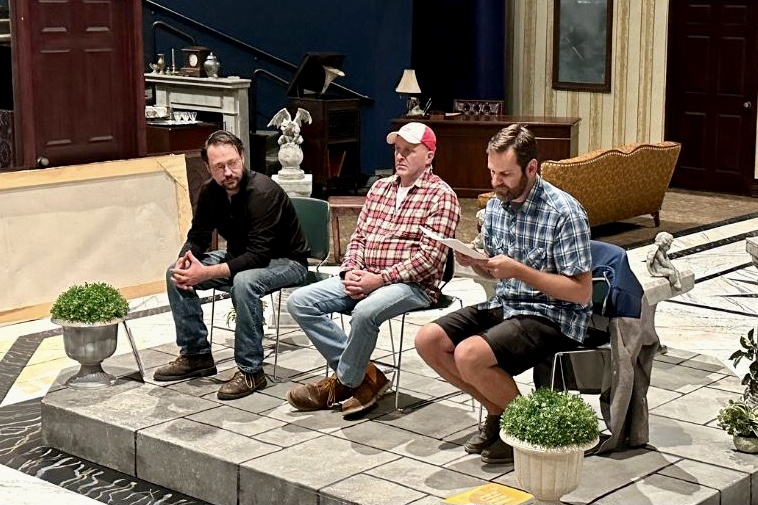
Have you ever sat at a performance and wondered what goes on behind the stage?
Here at MSU, even students who work on Department of Theatre productions rarely get a chance to see how all the technical elements come together and to learn about the underlying motivation for technical solutions supporting the artistic endeavors onstage in totality. Providing a comprehensive understanding of how all the scenic elements and effects came together to support our recent production of Clue, the Scene Shop faculty was inspired to host an in-depth technical seminar allowing for a start-to-finish discussion of this rarely seen endeavor.
It’s hard to quantify the amount of problem-solving that went into this production — in truth, all productions. A trap door, revolving bookshelf, multiple secret passageways, and a slow-motion falling chandelier are just the beginning of the logistical hurdles to clear, each of them needing careful consideration and planning to produce the desired effect safely, efficiently, and repeatedly.
Translating a show that is typically confined to the visual net of a proscenium arch becomes even more challenging on a large thrust stage such as Wharton’s Pasant Theatre where the audience sits on three sides of the action rather than directly in front. So, hiding the “magic” required out-of-the-box thinking. Pair this with a construction timeline of four weeks and you have the recipe for preparation, engineering, and problem-solving which mostly occurred solely between faculty during long nights and weekends. This process is what we hoped to explore with our technical seminar.
One secret to the theatrical “magic” on stage is the ability of designers and technicians to tap into solutions derived from other fields of study and industry. “Clue” was no different in this respect and we wanted to share this with students. The stage rigging used in theater is built upon a foundation of centuries of sailors utilizing ropes and knots hosting sails, securing equipment, and more. This, in turn, was modernized using technology developed to build suspension bridges and to string telephone wires across the country.
In Clue, we harnessed this past to deliver a chandelier falling towards the stage in slow motion. Pneumatics (with roots in the early days of the Industrial Revolution and prominent throughout modern manufacturing and automated equipment) were controlled below the stage that powered a trap door and a gargoyle statue that tipped over. In contrast, the revolving bookcase was actuated by a simple pulley mechanism—a very analogue solution dependent on quality carpentry and basic mechanics.
The seminar also included discussions on scheduling challenges, concepts in material usage, managing a dynamic and fast-paced construction and scenic painting workflow, and such stagehand essentials as how to safely manage large scenic pieces and the fundamentals of a counterweight rigging system. Though it was a lot to pack into a single day, the opportunity to provide insight into the complete production process and an in-depth look at the creative process through a technical lens was a rewarding endeavor that we hope will pay unlimited dividends for our students.
This Faculty Voice originally was published by MSU Today.